Get a quote for testing your samples
If your work involves formulation, process development or quality control of inks, paints or coatings then we would like to help you achieve your goals. Let us be your “Instant Physical Lab”, providing anything from ad-hoc sample testing to full Design-of-Experiments studies, using relevant and robust methods and with expert results-interpretation and support.
If you have your own in-house capability then we would be delighted to help you get the best out of your instruments with practical training, test method development and results interpretation advice.
The rheology and interfacial properties of inks, paints and coatings
The physical properties of inks, paints and coatings are critical material attributes for ease of handling, efficient processing, robust storage stability and effective application and performance. What follows are a few examples of the measurements we perform on these materials.
Zero-shear viscosity for physical stability
A key strategy for stabilizing a suspension or emulsion is to ensure immobilization of particles or droplets when the formulation is at rest, for example when on storage. Zero-shear viscosity can be thought of as the viscosity of a formulation when in this at-rest condition and therefore a high value will arrest the movement and impart better stability. Thixotropes, thickeners and inorganic stabilizers do their job by generating structure that in turn ramps up the zero-shear viscosity. Zero-shear viscosity cannot be measured using traditional viscometers such as the ICI Cone and Plate, Stormer Krebs or Brookfield viscometer but necessitate high performance rheometers such as those at the Centre for Industrial Rheology.

Wetting and spreading
Wetting of a surface during a coating process is a function of the aggregate effects of the liquid/solid interfacial tension driving the wetting and the liquid surface tension, viscosity, viscoelasticity, yield stress and thixotropic recovery resisting the process.
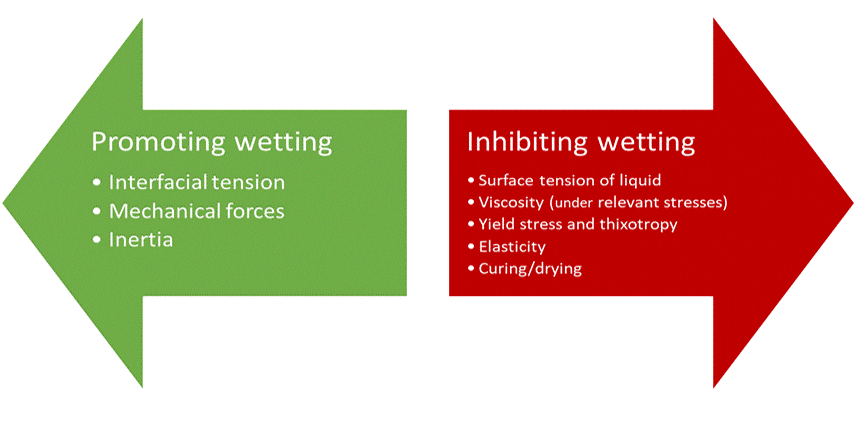
Surface and interfacial tension is dynamic, changing with the movement of surface active agents to and from an interface and coating rheology is complex, with non-Newtonian behaviour, structure and viscoelastic effects contributing similarly so. A dynamic wetting analysis and rheological profiling will elucidate some of the key factors that differentiate good and bad coatings.
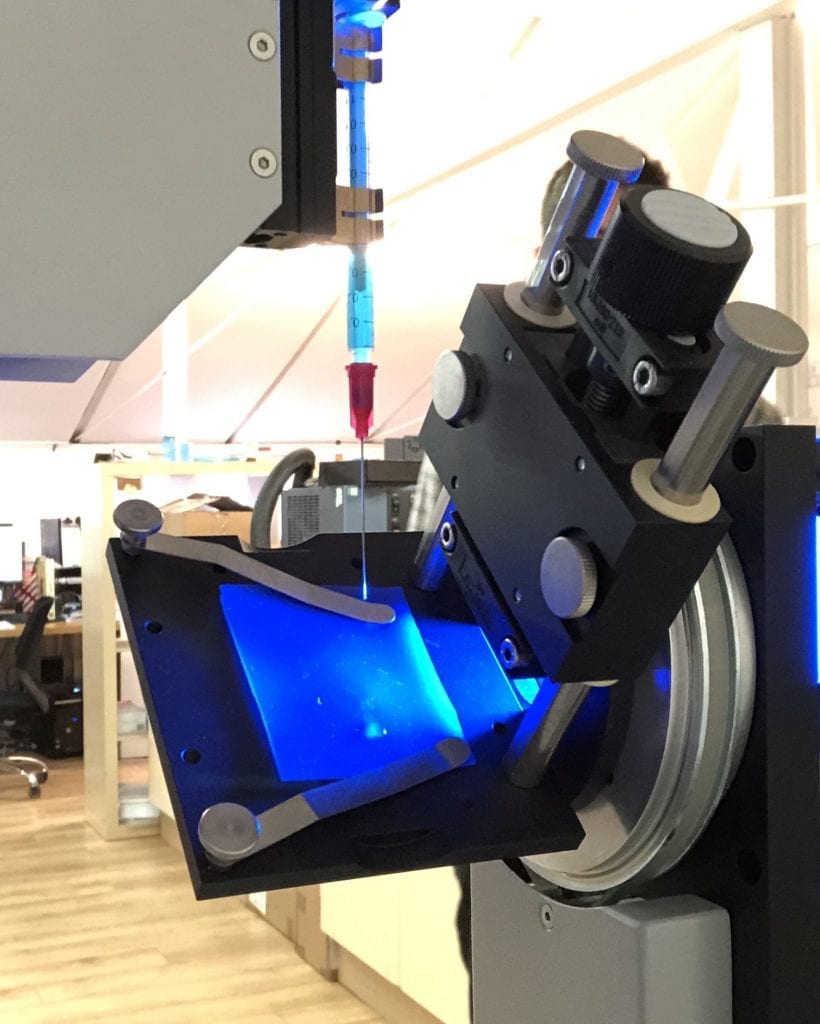
Sag and slump resistance and coat build
The ability for a coating to maintain a high build on a vertical or inclined surface and resist slumping and sagging when deposited on a horizontal surface is determined by the combined contributions of structure recovery (yield stress and thixotropy), viscosity under the relevant stress conditions and slip resistance/adhesion. A coating that undergoes a rapid return to a highly structured condition immediately following application will better resist sagging and slumping. Phase angle obtained from dynamic oscillatory measurements is a simple and reliable method of monitoring thixotropic recovery of coatings and inks. A low phase angle indicates an elastic response and is indicative of the presence of structure, so the rapidity of return to a low phase angle following a period of destructive shearing therefore serves as a simple indicator of thixotropic recovery rate.
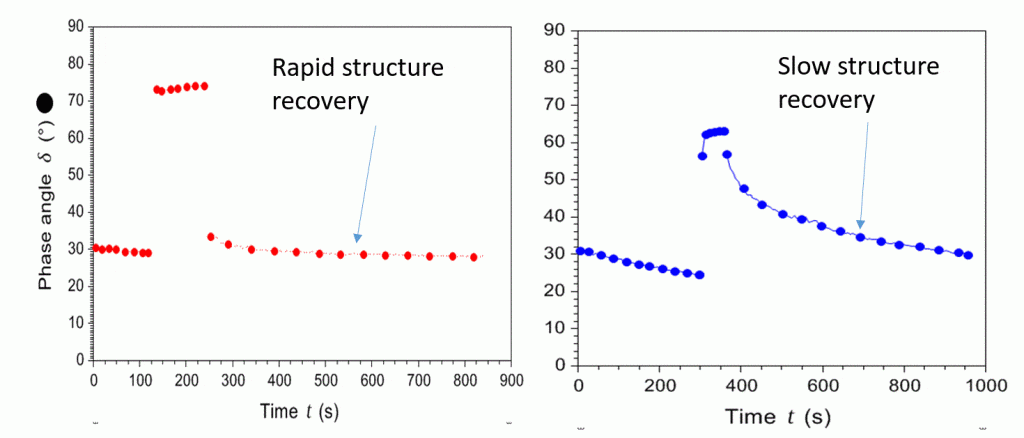
Levelling
Levelling of undulations from, for example, brush application, elasticity-related striping from blade coating or defects left by popping air bubbles is a process led primarily by surface tension. As with wetting and spreading, this process is also hampered by rheological properties, notably viscosity and the presence of a yield stress.
Atomization and spraying
For atomization to occur a formulation must shear down to a sufficiently low viscosity that it can be expelled at a suitable velocity from a nozzle. The combination of low viscosity and high nozzle velocity generates turbulent conditions to drive atomization. Countering this process is the possible presence of extensional viscous or elastic resistance that can inhibit the pinch-off process necessary for fine droplet formation. Viscosity and viscoelasticity profiles can help predict these behaviours.