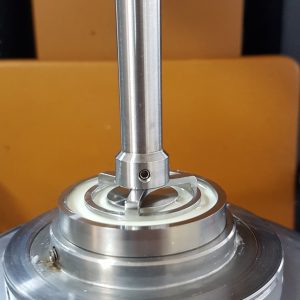
Curing of resins using UV light has been monitored using dynamic surface rheology, providing valuable insights including lag time between exposure to irradiation and the curing process starting, the rate at which curing occurs, and the strength of any film or structure made. This insight can provide valuable information to research and development scientists, marketing teams and formulators.
Contact us to arrange a lab tour and discuss rheological techniques with our experts
Dynamic surface rheology vs bulk rheology
In bulk rheology the sample is placed between two surfaces: the lower plate and the upper geometry. The central portion of the sample is effectively shielded from the external atmosphere, and any solvent evaporation or losses are minimised. This is perfect for the centre of a bulk material, but in situations where solvent losses occur, or where a product is required to cure in the open air, a realistic profile of rheological behaviour at the surface of a material may not necessarily be captured.
Dynamic surface rheology is a complementary technique to ‘traditional’ bulk rheology. It allows for collection of data when exposure to air or an external atmosphere is required for a change in the material’s properties at the surface, for example during film formation or when drying. The sample is loaded into a lower trough and a ring-geometry is lowered onto the sample’s surface such that the ring is just in contact. If a film is formed, the ring is incorporated into the film. This approach allows direct measurement of a surface or film’s characteristics e.g. change in viscosity or complex modulus over time due to curing or solvent evaporation. In addition, because the ring is incorporated into the film, the strength of a film after formation can also be investigated.
Measuring the UV curing of films
Curing films using UV light is rapid, does not require elevated temperature, and can provide a large degree of control over when the material cures, as curing only occurs in the presence of UV irradiation. Monitoring the rate of cure, the lag between commencement of irradiation and physical changes of the material, the strength of any film prepared, or even simply benchmarking products against each other can provide valuable information to research and development scientists, marketing teams and formulators.
We took four resins (A–D) that are cured under UV irradiation (395 nm) and subjected them to testing using our dynamic surface rheometry attachment. The photoinitiator for each of the resins was varied and the UV light source was approximately 10 cm away from the resin’s surface. In resins A and D the photoinitiator was a phosphine oxide, in resin B it was a thioxanthone and in resin C it was a benzophenone-type. In all cases the depth of resin cured was approximately 3 mm.
The use of an oscillatory mode allowed for monitoring of the rigidity of the surface, providing information about the properties of the resin before and after curing. For all experiments oscillation was started and then the UV light was turned on after 30 seconds. Once the sample was subjected to irradiation there was a clear up-tick in the complex modulus value showing that the material was becoming more rigid, Figure 1.
When cured, resins A and D formed a polymeric network across the bulk and a disk was isolated from the geometry after the experiment. Resin B formed a thinner film, where there was a small residue of uncured material remaining, and resin C formed the thinnest film with a large reservoir of uncured resin underneath the film formed. During curing resins B and C both became yellow, which is a known issue with thioxanthone and benzophenone-type photoinitiators. This is known to retard film-forming processes, especially for thicker films because it blocks the UV penetration. This poor curing likely affected the final film rigidity, with the resins that cured to a thinner layer forming a less rigid structure.
The rate at which curing occurred, either as a film (in the case of resins B and C) or of the bulk (in the case of resins A and D) was variable, and resins A and D cured the most quickly followed by resin B and then resin C. The rigidity of the cured product was also variable. Once cured and the complex modulus had reached a maximum, resins A, B and D had a similar rigidity, but sample C was markedly less rigid. Again, this is likely related to the photoinitiator used and interactions between the UV light and photoinitiator itself.
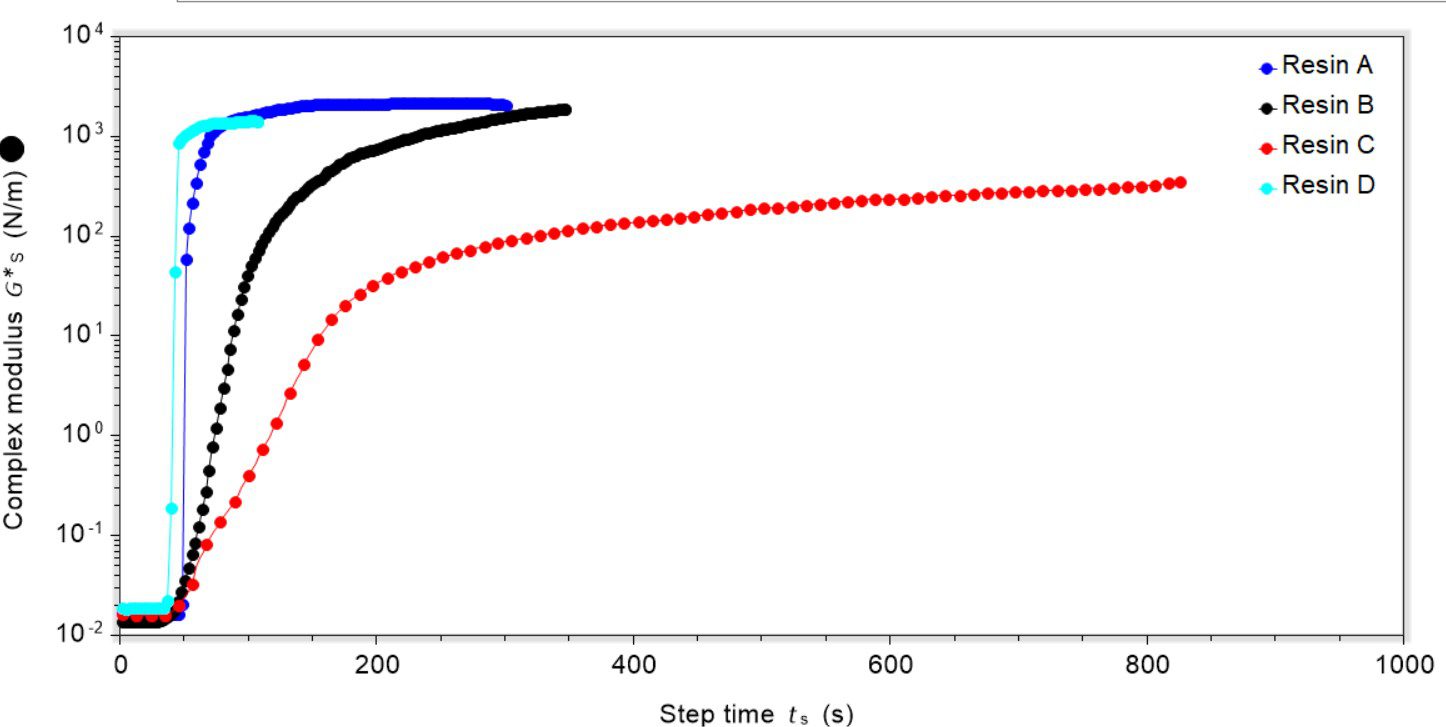
Quantifying curing rate and lag
Looking more closely at the time-point at which irradiation started, differences in the lag between irradiation starting and curing commencing can be seen. In all cases, irradiation was started 30 seconds after the oscillatory experiment was started, Figure 2. Resin D had the shortest lag between irradiation starting and curing commencing (36.4 secs), with resins B and C next and resin A having the longest lag (45.4 secs).
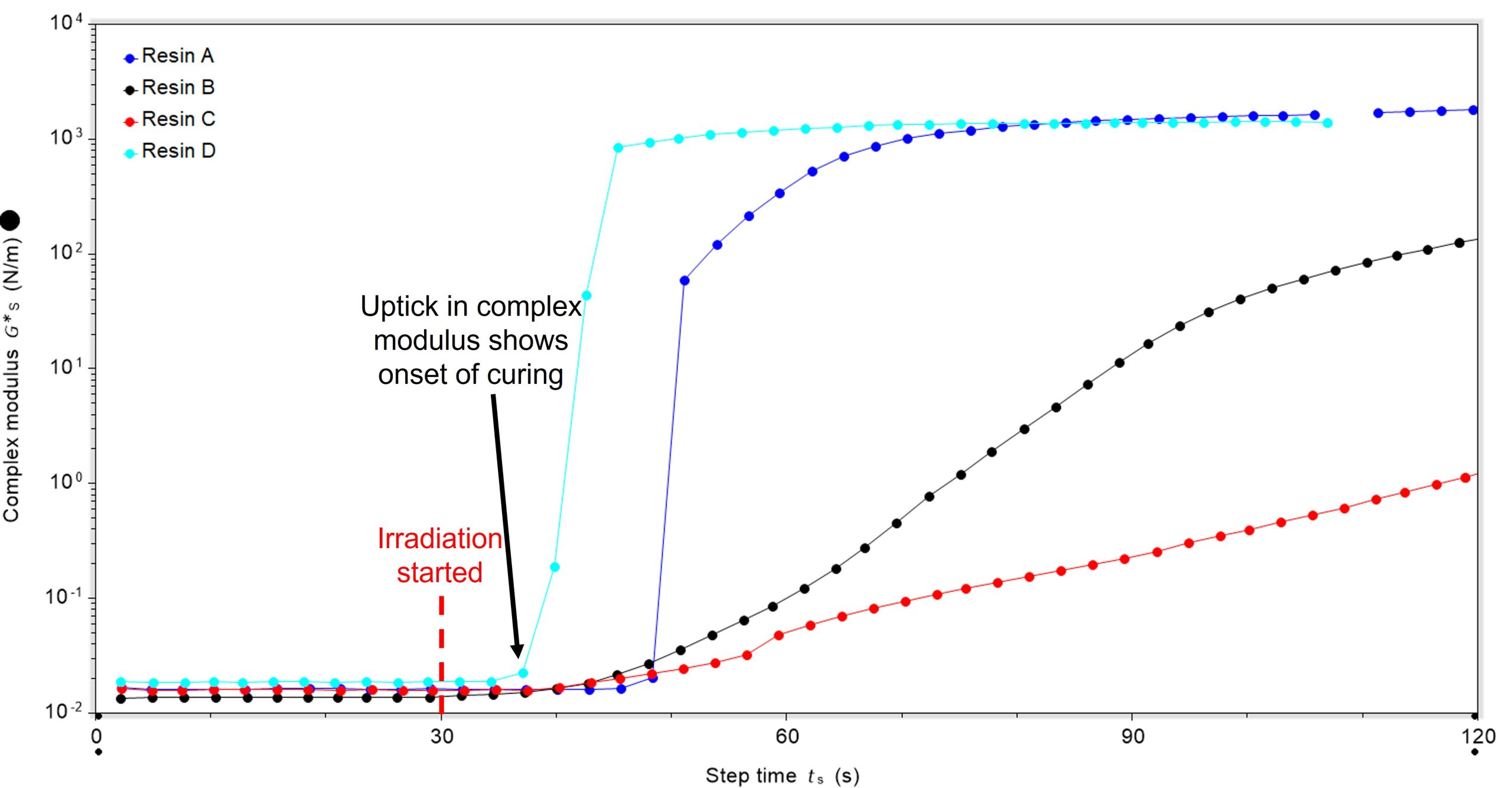
It was also possible to quantify the initial rate of curing. Resin A cured at the fastest rate, once curing was initiated, and resin C was the slowest. Interestingly, the rate of cure for all samples slowed as the reaction neared completion, Figure 3.
Resin | Initial rate of curing (Nm–1s–1) |
A | 1.25 |
B | 0.07 |
C | 0.02 |
D | 0.58 |
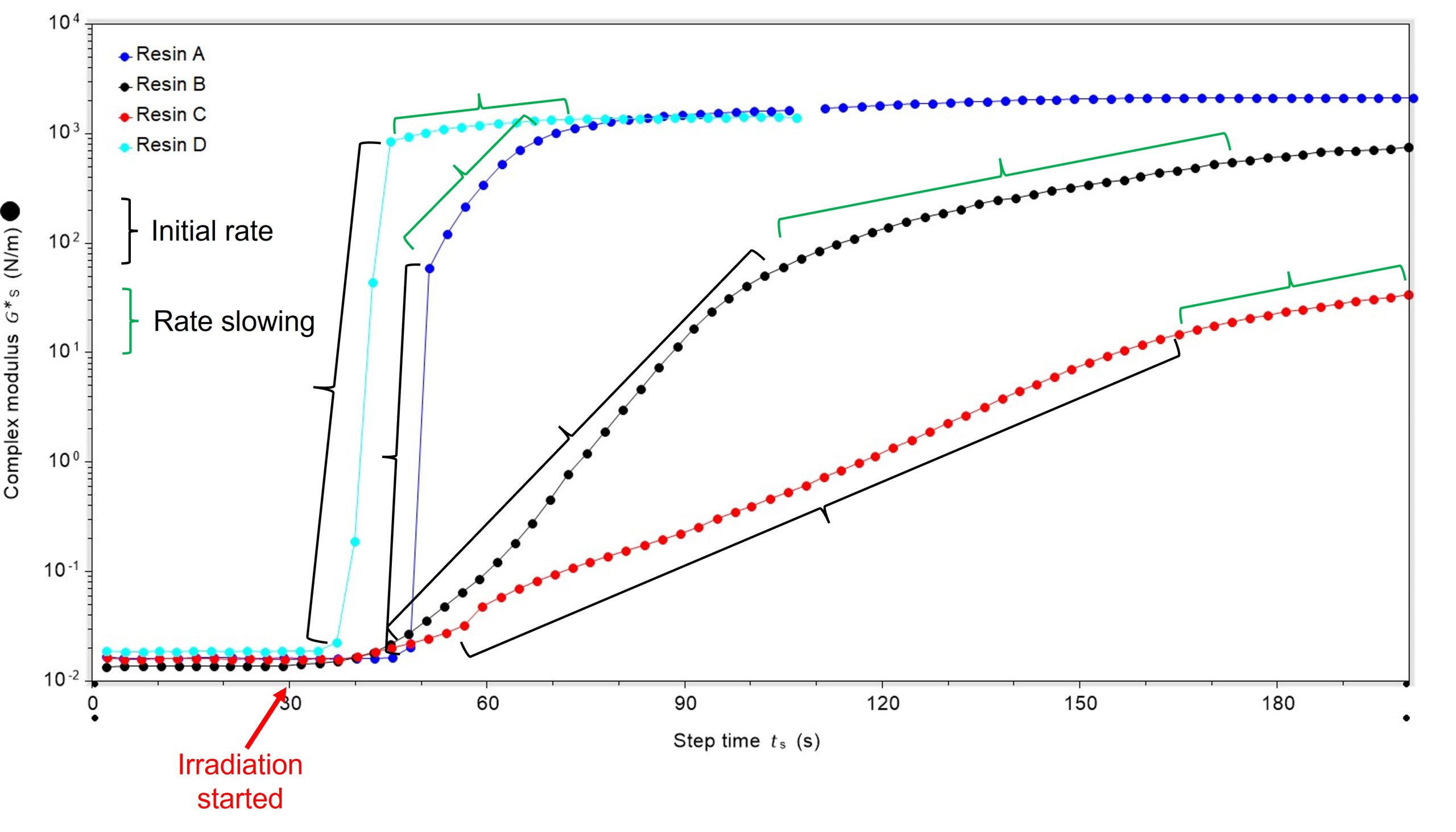
Summary
In summary, the use of dynamic surface rheology to monitor UV curing of resins provides valuable insights into curing of films using UV irradiation. One of the major advantages of this new technique is that the sample is open to the atmosphere and changes that would occur during a ‘real life’ application where a cure or drying process happens can be monitored.
Core findings include:
- Phosphine-oxide based photoinitiators led to more rapid curing than the thioxanthone and benzophenone-type photoinitiators studied.
- Phosphine-oxide based photoinitiators led to formation of a stronger, thicker film overall compared with the thioxanthone and benzophenone-type photoinitiators studied.
- Both the benzophenone-type and thioxanthone initiators studied yellowed over their exposure to UV light. In the case of the benzophenone-type photoinitiator, this yellowing led to a retarded rate of film formation and a significantly less rigid film compared to the other formulations studied.
For information about the testing performed here, or to talk about other ways that we can help with rheological testing, please get in touch.