Rheology and surface tension both play a key part in the formation and prevention of coating defects. While simple viscosity measurements are often used to check for and pre-empt coating defects, they can misrepresent underlying causes. Often the cause of these coating defects is due to a number of rheological properties not easily measurable with a simple viscometer.
Contact us to discuss coating issues you are encountering, and the best methods to understand this behaviour
Getting to the root cause of a coating defect can save time, money and resources. At best, coating defects can manifest as unsightly visual manifestations, and at worst can cost millions in expended materials and loss of performance. Important rheological factors like viscosity, thixotropy, surface tension and yield stress can provide vital information to chemists, engineers and applicators looking to modify their formulations and processes in order to avoid the emergence of defects. At the Centre for Industrial Rheology, we perform a wide range of rheological testing to help formulators, manufacturers and applicators minimise or eliminate coating defects.
DEFECT | Symptoms | Viscosity | Thixotropy | Cure Time | Surface Tension | Yield Stress | Extensional Viscosity |
---|---|---|---|---|---|---|---|
Bubbles | Bubbles, Blisters, Craters and Pinholes | ✓ | ✓ | ✓ | ✓ | ✓ | |
Streaks | Areas of reduced coating thickness. | ✓ | ✓ | ✓ | ✓ | ||
Ribbing/ Chattering | Areas of varied coating thickness the whole length/width of the coating. | ✓ | ✓ | ✓ | ✓ | ||
Edge Defects | Areas of increased coating thickness at the edges of the coated area. | ✓ | ✓ | ✓ | ✓ | ✓ | |
Neck-in | Decreased Coating width along length of substrate. | ✓ | ✓ | ||||
Orange Peel | Areas if reduced coating thickness across the entire coated area (similar to the skin of an orange) | ✓ | ✓ | ✓ | ✓ | ||
Runs/ Sags | Downward movement of coating on a vertical surface | ✓ | ✓ | ✓ | ✓ | ||
Crawling/ Creep | Unwanted spread of the coating outside of the desired area | ✓ | ✓ | ✓ | ✓ | ||
Wrinkling/ Crowsfooting | Areas of increased coating thickness at the edges of the coated area. | ✓ | ✓ | ✓ | |||
Solvent Pop | Similar to bubbles, caused by escaping solvent rather than trapped air. | ✓ | ✓ | ✓ | ✓ |
Viscosity – Your First Port of Call for Examining Coating Defects
Viscosity describes a material’s resistance to flow and is pivotal in all stages of the coating process, causing or minimising a wide range of defects.
High viscosity coatings can be problematic to spray, pickup or deposit onto a substrate. A low viscosity coating can potentially level well, filling in holes or streaks in the coating, but can also lead to unwanted creep/spreading.
Coating defects can be further complicated by non-Newtonian behaviour whereby the viscosity changes as a function of the applied shear to the material. Shear thinning is the most commonly observed non-Newtonian behaviour, when increasing shear causes a drop in viscosity.
Yield Stress – A Key Indicator For Bubbles, Streaks And Sags
Yield stress represents the amount of stress required to cause a material to flow significantly. While we may not think of coatings as “solid”, many do in fact exhibit structured, solid like behaviour as a result of inter-particle and/or polymer interactions.
A key indicator for this solid structure is the coating’s “bounce-back-ability”, an elastic response that can be detected using oscillatory testing methods. Yield stress is a measure of the stress that must be applied to disrupt this structure and elicit significant flow. A high yield stress can be particularly useful for preventing bleeding or spreading and keeping lines defined.
Thixotropy – How Does Your Applicator Change Your Coating?
Most methods of application are relatively high shear processes, and are rare events considering a coating spends the majority of its life at rest (either sitting in container under storage, or on a surface immediately after application).
The thixotropic recovery rate describes the speed at which a material returns to its original viscosity after it has been sheared. This can cause issues if the viscosity of a coating drops during application and remains low after having been deposited on a surface. In extreme circumstances, a coating that recovers rapidly may not self-level as efficiently.
Surface Tension – Adhesion, Wettability and Droplet Formation
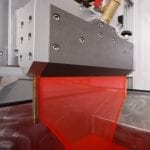
In general, liquids exhibit a tendency to maintain as least as possible surface area, due to attractive forces between molecules. This attraction known as surface tension has a significant influence on the wetting properties of coatings, droplet formation during spraying, and application through dies.
The ability of a coating to wet a surface is vital to achieving a uniform and defect free coated layer and depends both on the surface tension of the coating, and the surface free energy of the substrate. Achieving a good balance between the two will aid in avoiding defects, such as crawling, craters, and fish eyes.
Cure Time/Skin Formation – Avoiding Bubbles and Craters
The cure time of a coating refers to the time it takes to harden once applied, be it by air drying or a two part chemical cure. In the case of air drying, curing begins on the surface of the coating most easily accessible by the surrounding air. This tends to be at edges of the coating where the surface area of the coating is at its greatest.
Incorrect cure times can cause a myriad of issues, from wrinkles and crows-footing, to orange-peeling and mottling. Skin formation happens at the very start of an air cure, where the uppermost layer of the coating is beginning to cure. If this layer forms too fast, it can prevent air bubbles or evaporated solvent from leaving, or cause the skin to burst as they leave.