We can identify how specific process parameters such as applied shear or various temperatures can affect the quality of your polymer melt during processing. Our lab is equipped with both a high temperature oven (500°C) and nitrogen purge system for investigating temperature driven changes in rheology of your polymer including depolymerisation, polymerisation and oxidation. Contact us to discuss how we can help investigate thermal degradation of your polymers.
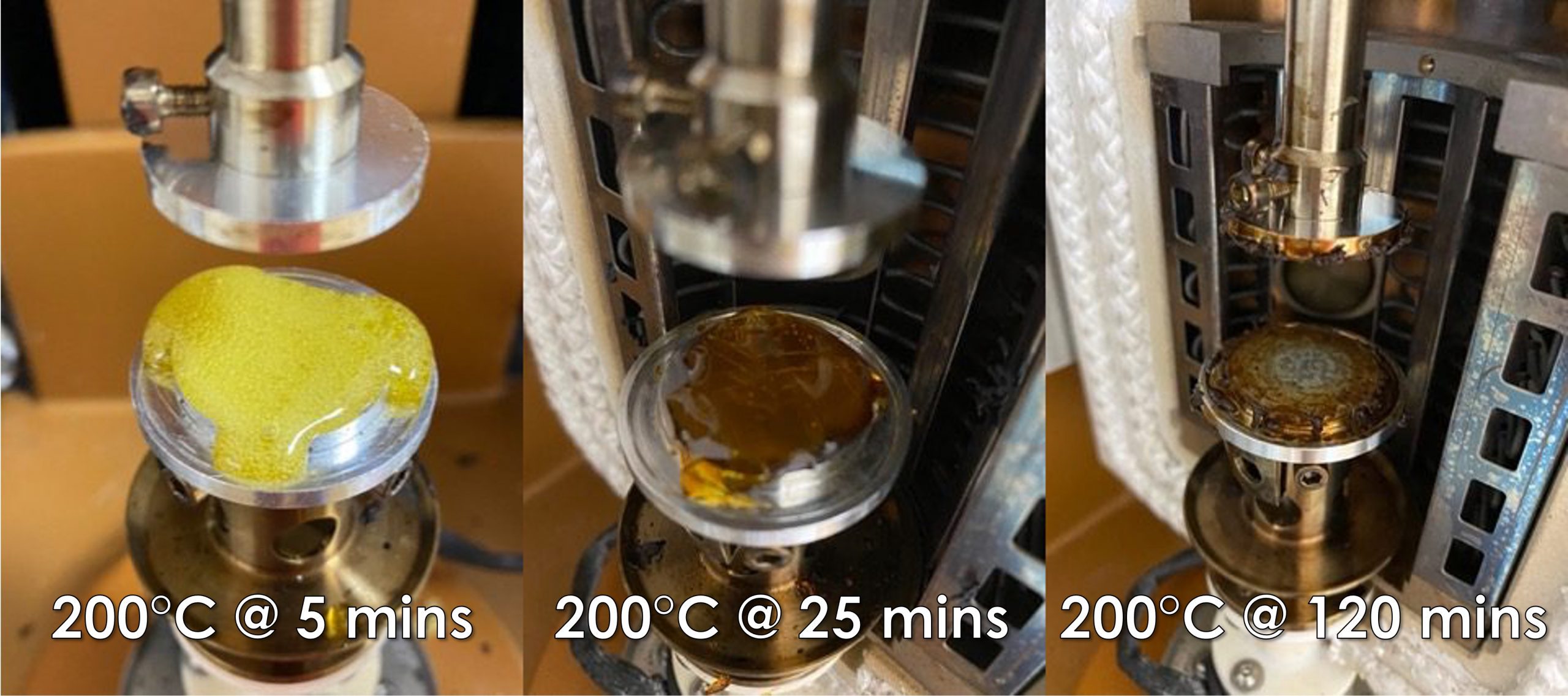
Contact us to learn more about our thermal degradation of polymers capabilities,
High temperature oxidation is a common problem when working with certain polymer melts at high temperature. Oxidation can cause discoloration or changes in quality and performance of a polymer material, making it unsuitable for its initial use.
For some elastomers, a combination of high temperature and water content can cause chain scission or further polymerisation. This becomes a difficult problem to solve if the melt temperature of the material occurs within the boundary that these chemical processes occur.
Oscillatory Time Sweeps and Temperature Cycling for Thermal Degradation
In an oscillatory time sweep, the response to deformation of small amplitude oscillations are tracked over time to quantify the rate of change in the material under a specific condition. E.g. at prolonged high temperatures in an air environment vs. an inert gas environment. This can be very useful for tracking the stability of a sample while it is in a specific environment and getting a rate of change.
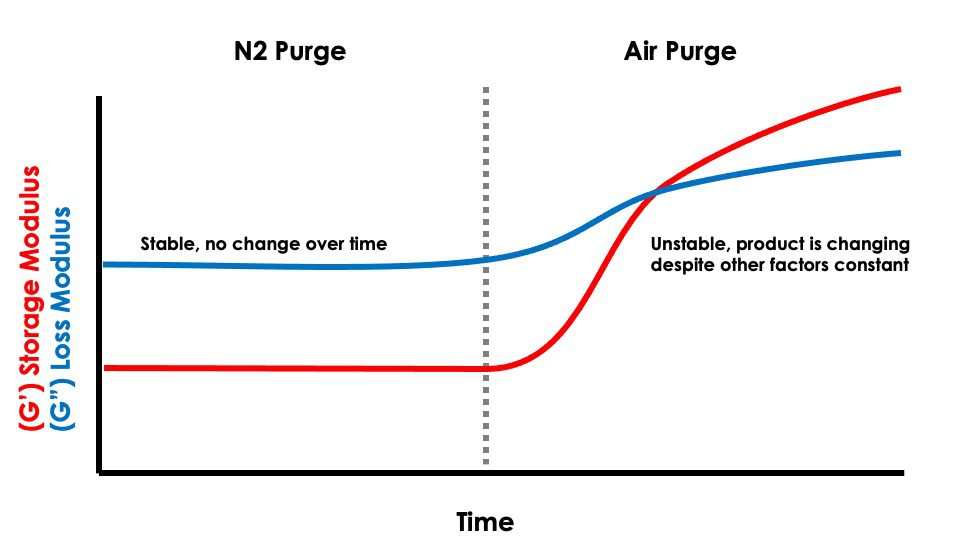
A temperature cycling test as the name suggests, involves ramping the temperature between a high and low value for a set number of cycles over a set period of time (generally limited by the rate it takes for a sample to reach thermal equilibrium with the heating chamber). Comparing the gradient and peaks of each cycle can give you an idea of the robustness of the material as temperature is repeatedly cycled. You can also compare the material in an inert gas environment against its less than ideal operating conditions and quantify the extent the conditions degrade the rheological behaviour of the polymer.
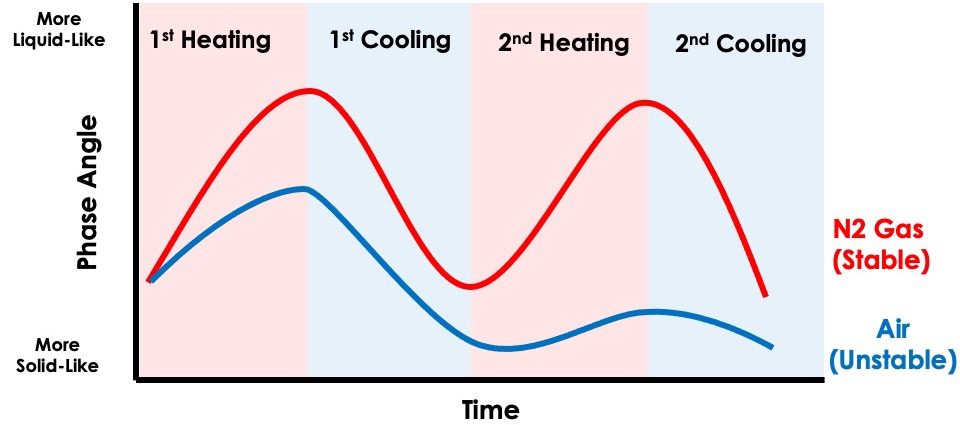
High temperature oscillatory frequency sweeps for a before and after snapshot
High shear rheology for some polymer melts can sometimes be practically challenging. Due to the high strain involved, the measurement itself can damage the sample or cause it to fail at the edges, providing erroneous results. Oscillatory frequency sweeps are the preferred method for characterising polymers in the melt condition due to the low strains involved, and the ability to relate data back to microstructural properties including average molecular weight and average molecular weight distribution.
The high sensitivity of oscillatory rheometers makes them suitable for early detection of physicochemical changes occurring within the polymer, such as change in molecular weight average or molecular weight distribution. The maximum of storage modulus is a good indicator of molecular weight distribution, with higher values indicating a narrow distribution and lower values indicating a broad distribution.
If the storage modulus-loss modulus crossover point occurs at a lower frequency than the benchmark, it indicates the sample possesses a higher molecular weight average. A crossover point that occurs towards the right of angular frequency indicates a material with a lower molecular weight.
Cox-Merz Relationship for Viscosity
The Cox-Merz relationship describes an empirically-observed equivalence, for some qualifying products, between complex viscosity values obtained from an oscillatory frequency sweep and viscosity values obtained from a shear rate sweep. Qualifying products tend to be polymer melts along with concentrated polymer solutions. Dispersions deviate from the observed behaviour.
The zero-shear viscosity, or plateau viscosity is a highly sensitive way of measuring molecular weight of high molecular weight polymers, the viscosity being proportional to molecular weight, MW3.4 . In addition to observing the zero-shear plateau, the onset of non-Newtonian behaviour (generally shear thinning) is an indicator of the distribution, with early onset generally being related to a broad distribution.