Sealants are common building materials that usually contain silicone-based polymers and are generally used to prevent fluid ingress, often in a bathroom or kitchen. Key requirements for sealants are that they can resist water ingress, are resistant to moderate deformation, and can flow under pressure but quickly regain their structure once the pressure is removed while resisting creep or sag. Rheology can be used to investigate these desirable properties and has been used to benchmark several commercially available sealants against each other.
Contact us to arrange a lab tour and discuss rheological techniques with our experts
Sealant chemistry
Most building materials used in kitchens and bathrooms use sealants and are based upon silicone, which is a polymer formed from many siloxane (–R2Si–O–SiR2–) units. The chemical composition of the siloxane units can be varied, for example by incorporating more cross-linking, amending side-groups and introducing cyclic species, which can all affect the final properties of the material.
The siloxane-containing materials used within the bathroom and kitchen sealant industry are often thick liquids that are rubbery in texture when dried. In addition, they are water-repellent, durable and can inhibit microbial growth.
Household sealants are usually applied using a caulk gun. With this mode of application, the sealant is forced out of a nozzle and placed directly upon the intended substrate. The rheological demands upon this material are numerous:
- In order for the material to be gunned onto a substrate, the yield stress needs to be overcome to disrupt the structure and render the material flowable;
- Not only does the material need to start moving in the cartridge, it also needs to overcome the stress needed to enter the smaller nozzle;
- Furthermore, any extensional viscosity that may prevent the sample entering the nozzle also needs to be overcome;
- However, once the material is flowing and has been applied to the substrate it needs to recover its structure quickly so it does not ooze (known as thixotropic recovery);
- The material should not slump or sag once it has been applied.
Rheological characterisation can be used to probe a number of these properties and provide a metrics-based process for comparing and contrasting different formulations or products.
Studying sealant characteristics : flowability, structure and thixotropic recovery
This study compared the flowability, structure and thixotropic recovery of five commercially available sealants using rheological techniques. The first test that was completed was a controlled rate viscosity profile (CRVP), which would allow for observation of changes in viscosity in relation to the shear rate, Figure 1.
- Sealant A – a low modulus, neutral-curing silicone sealant
- Sealant B – a mid modulus sanitary and shower silicone
- Sealant C – a mid modulus sanitary and shower silicone
- Sealant D – an acetoxy silicone containing fungicide
- Sealant E – an acetoxy silicone for use in hot and humid environments
All samples could be described as non-Newtonian and shear thinning however, although due to the logarithmic scale it looks like there are minimal differences in the data, closer scrutiny reveals that the viscosity of Sealants A, B and C are almost twice as high as that of Sealant D. Practically, this means that Sealants A, B and C will require twice as much stress to maintain movement, and therefore use of the sample, compared with Sealant D, which may have an impact upon consumer perception and ease of use.
Figure 1: Controlled rate viscosity profiles can reveal changes in viscosity in relation to shear rate
The next test was an oscillatory stress sweep, which provides data such as complex modulus and phase angle. The complex modulus allows for comparison of rigidity between samples. As well as comparing rigidity, it is possible the identify the point at which stress causes the breakdown of structure by determining the point at which the complex modulus starts to decrease.
The oscillatory data revealed that sealant E was the most rigid and sealants A and D were the least rigid, although at low stresses the rigidity difference between samples was minimal, Figure 2. However, the point at which oscillation stress caused structural breakdown was different for each sample. Sealants A, B and C required a similar application of stress to breakdown the structure, whereas sealants D and E required considerably less stress (indicated by the substantial decline in complex modulus value).
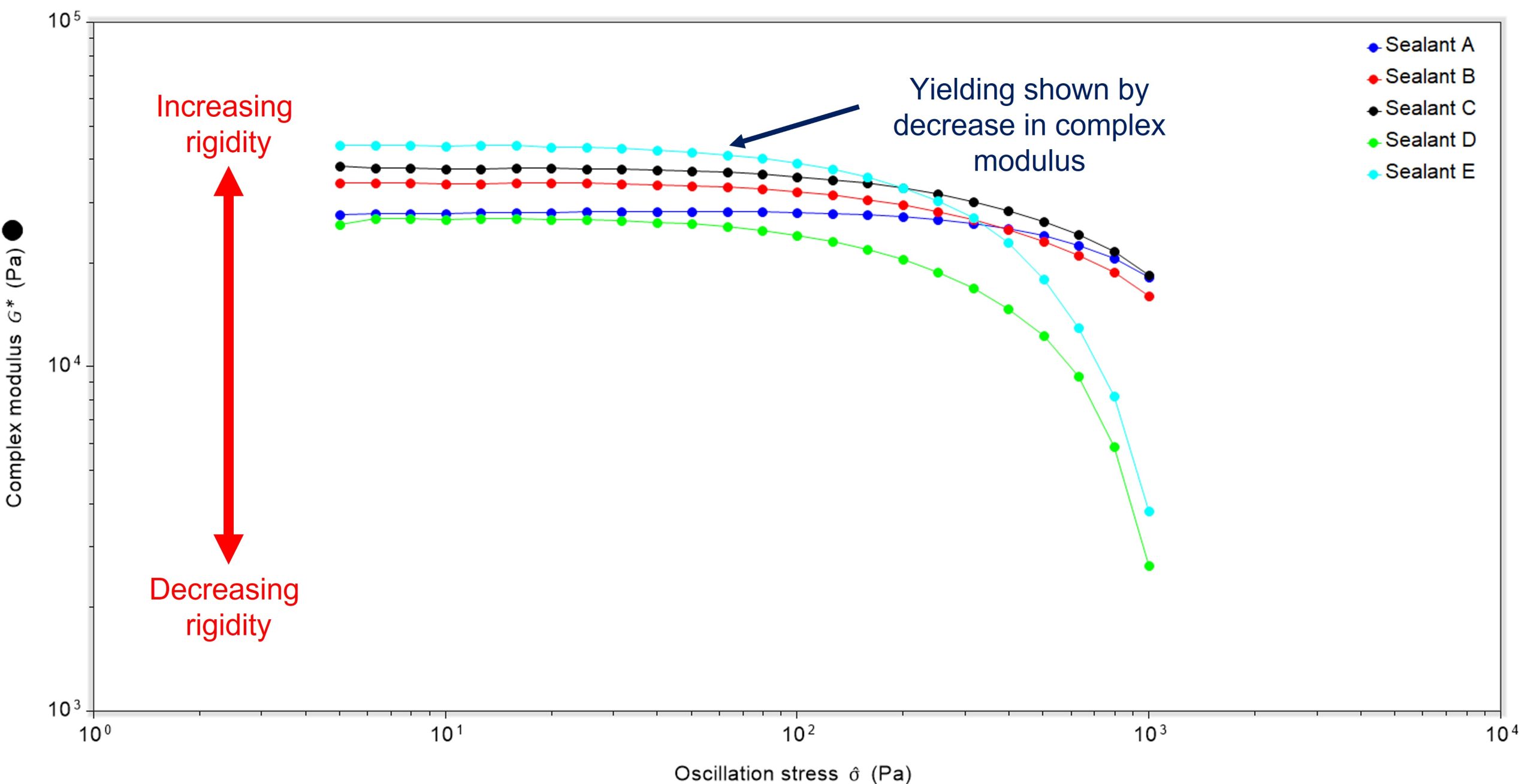
Phase angle data, also collected from an oscillatory stress sweep, can provide information about the state of the material under different stresses, Figure 3. Phase angle data is a useful way to visually show the difference in yield stress between samples and the change in behaviour prior to, or after, yielding. A phase angle below 45° shows solid dominance, and above 45° shows liquid dominance. The yield point can either be taken as the point at which the sample starts to change behaviour (i.e., the curve starts to deviate from the plateau), or the stress when the phase angle is 45°.
In this case, as the shear rate increased sealants D and E tended towards liquid-dominant behaviour but sealants A – C maintained a significant degree of solid characteristics. This means that sealants D and E start to yield at lower stresses, so are likely to be easier to gun and therefore apply. However, because D and E require lower yield stresses to flow, there is a danger that once D and E are applied they may undergo sagging or slumping which are both undesirable processes.

Thixotropy is a time-dependent shear-thinning property. Undertaking a thixotropy study allows for monitoring materials’ behaviour before and after the application of an external stimulus, for examples oscillatory or rotational shear. A thixotropy study was undertaken on the samples in this study, Figure 4. Samples were all exposed to low oscillatory shear (0.1% strain) for 60 seconds followed by high shear to disrupt the structure (500% strain) for 60 seconds, then low oscillatory shear (0.1% strain) for 300 seconds. This allows for changes in the rigidity of the structure to be observed, and also how quickly the material recovers its original structure.
Before significant oscillatory strain was applied, sealants A, B and C had a very similar rigidity and sealants D and E were outliers. During high oscillation the samples all became less rigid, and again sealants D and E were outliers, with a much lower complex modulus than the other samples. The final step was low oscillation. Interestingly, none of the samples recovered the sample rigidity that they had before the structure was disrupted, even after 300 seconds. Sealants B, C, D and E recovered the largest degree of rigidity in comparison to the structure of the material before oscillation, but sealant A remained significantly less rigid than the initial value. This means that after the Sealant A has been subjects to external forces, it may not recover the same structural rigidity that it had while at rest in the container.
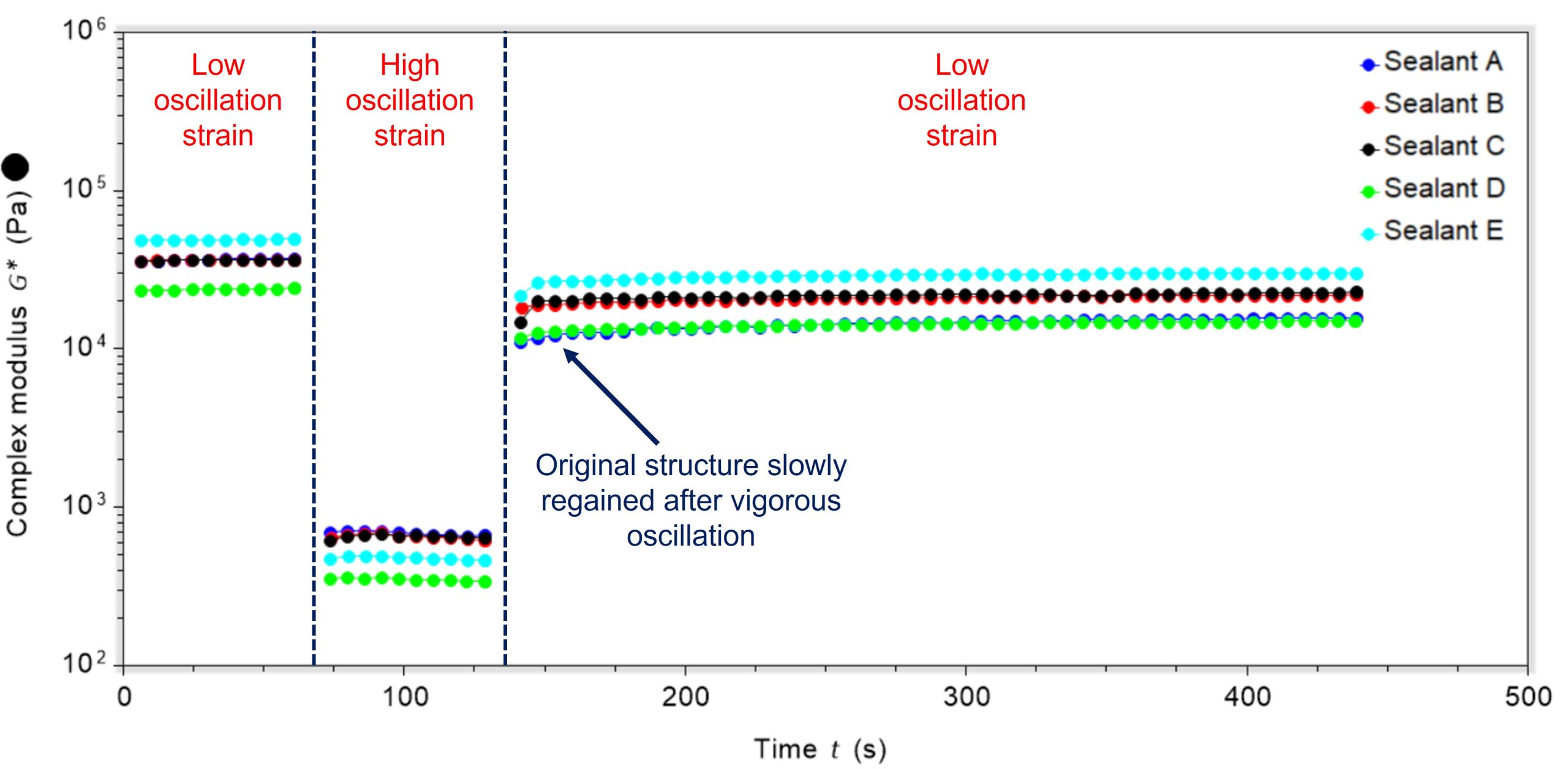
Summary
Rheology measurements have been employed to probe the properties of five commercially available bathroom sealants. All samples could be described as non-Newtonian and shear-thinning, as determined by a controlled rate viscosity profile. Oscillatory testing revealed differences in the rigidity and gunnability of the samples. These properties are important as they relate to the customer’s perception of the sample; if the material is rigid and has a high yield stress the customer will not be able to gun the material easily and application may be messy. On the other hand, if the yield stress is too low the product may sag or slump when applied.
For further information about characterising building materials rheology, and other related studies, please get in contact.