This case study demonstrates the application of Dynamic Powder Flowability measurements to predict the caking of pharmaceutical powders, specifically paracetamol powder caking.
Nowhere else does the potential for powder caking pose a greater concern than in pharmaceuticals – where ingredients are expensive, and processing is delicate and time consuming. Expenses can escalate rapidly when a product is no longer fit for purpose, and production is slowed due to a once flowable powder becoming an un-processable cake.
Our Lab Technicians at the Centre for Industrial Rheology examined a single pharmaceutical powder blend, subjected to 90% RH at 25°C, at several time points. We have investigated the influence of a “drying” step at a lower humidity, compared to the main conditioning step, to encourage the formation of solid bridges, which lead to powder caking. We were successful in capturing multiple key parameters which help to explore the caking profile of a powder, including the degree to which a powder cakes and the format that the cake takes throughout the powder bulk, from crusting to formation of agglomerates.
Contact us to arrange a lab tour and discuss rheological techniques with our experts
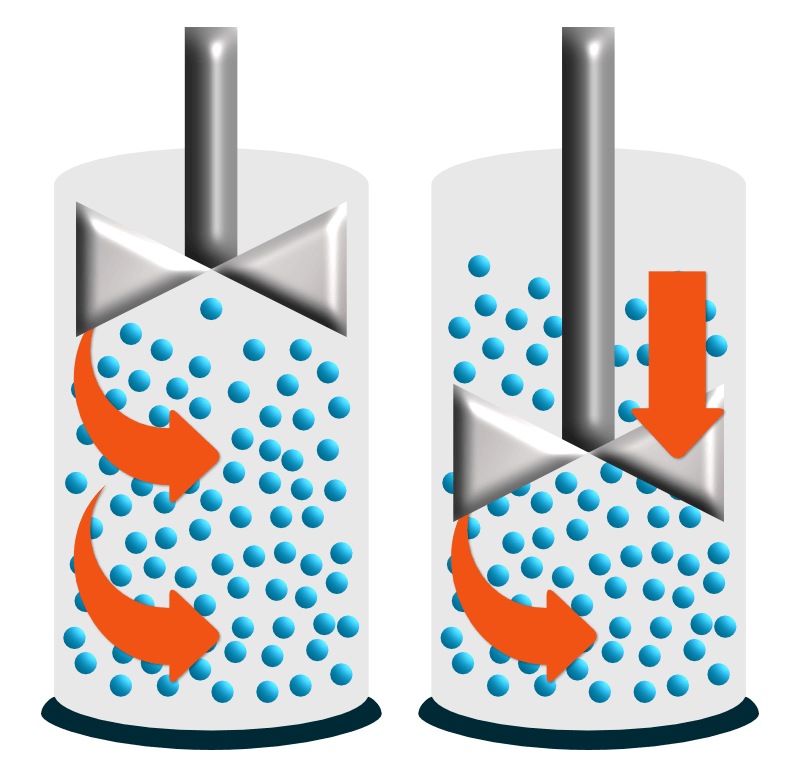
Dynamic Powder Flowability and Stability Measurement
Dynamic powder flowability testing is frequently utilised in pharmaceuticals to probe a wide range of powder behaviours. Its inherent similarity to a number of processing scenarios, coupled with the sensitivity of the methodology, have enabled characterisations of behaviours which were previously the sole domain of trial and error. From segregation to tablet capping, to wet granulation end point, variations on the dynamic flowability test have helped inform researchers, formulators, and process designers across a range of pharmaceutical applications and beyond.
Multiple measurements performed on a single sample at a single defined tip speed constitute a stability measurement. Stability measurements identify ongoing changes in a sample through processes such as aeration and de-aeration, segregation, and the breakdown of agglomerates.
Stability measurements of this kind have been utilised to examine powder characteristics such as aeration and de-aeration, segregation, and breakdown of agglomerates. In this study, we explore an approach that utilises this methodology to quantify powder caking behaviours.
For more information about powder characterisation, see this article.
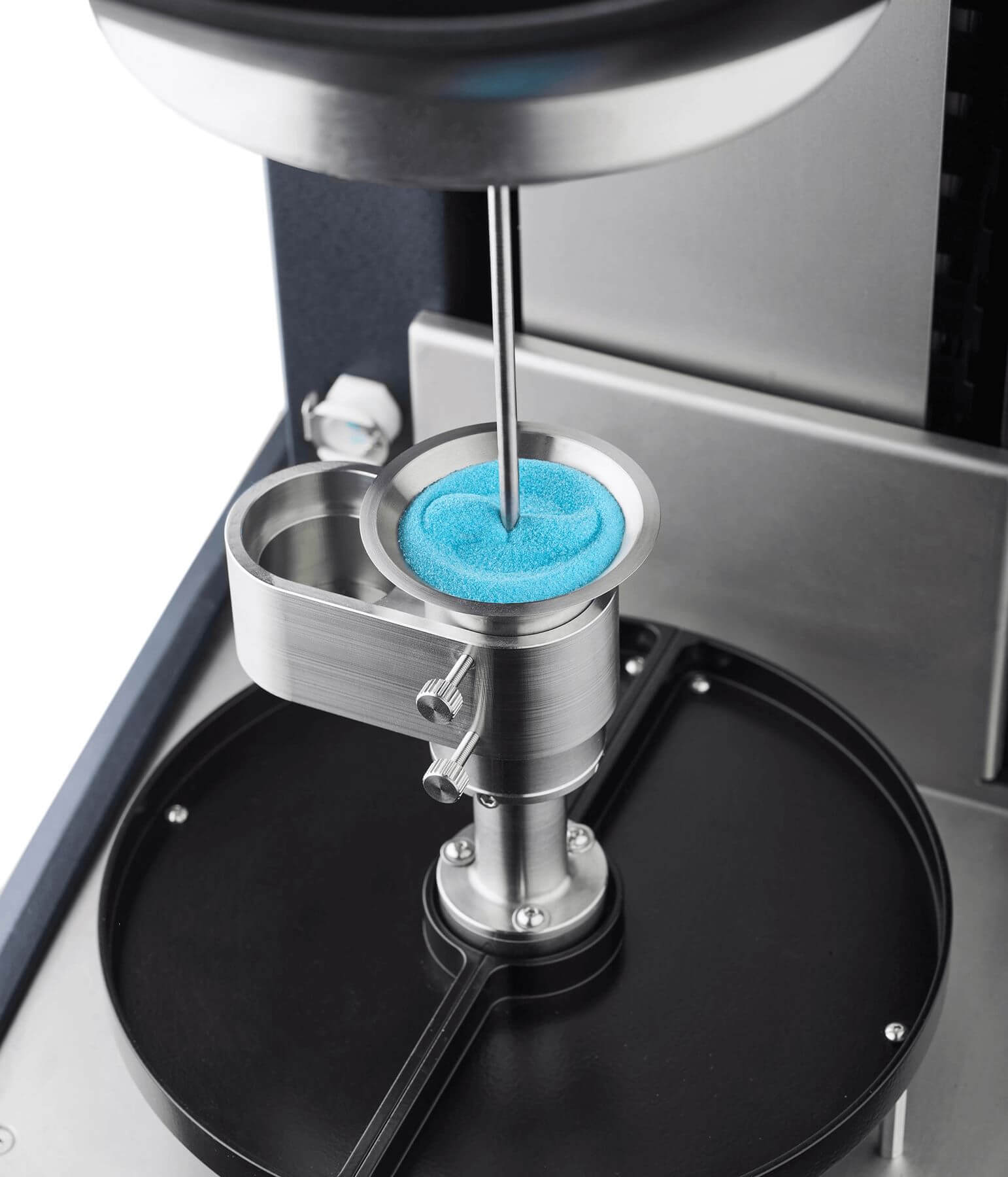
Kinetic and Humidity Conditioning Steps
Dynamic powder flowability measurements often employ a conditioning step immediately prior to measurement in order to improve reproducibility. This “kinetic conditioning” employs the same bladed geometry as the testing steps, rotating counter to the direction of the main measurement to gently reset the handling history of the powder.
In the course of this study, a second conditioning step is also employed. The sample is held in a climatic chamber for set periods of time at an elevated humidity. Importantly, where this humidity conditioning step is employed, it is performed:
- Following the kinetic conditioning step, in order to enhance repeatability between measurements and;
- In the vessel in which the sample it to be ultimately tested, in order to remove the need for disturbance of the sample between conditioning and testing.
Humidity conditioning following kinetic conditioning essentially strives to provide each aliquot of powder with a level playing field. Particularly when looking at caking, a main driver for which is often the formation of liquid and solid bridges at the contact point between powder particles, ensuring that the packaging state of the powder is as even as possible between test conditions is essential.
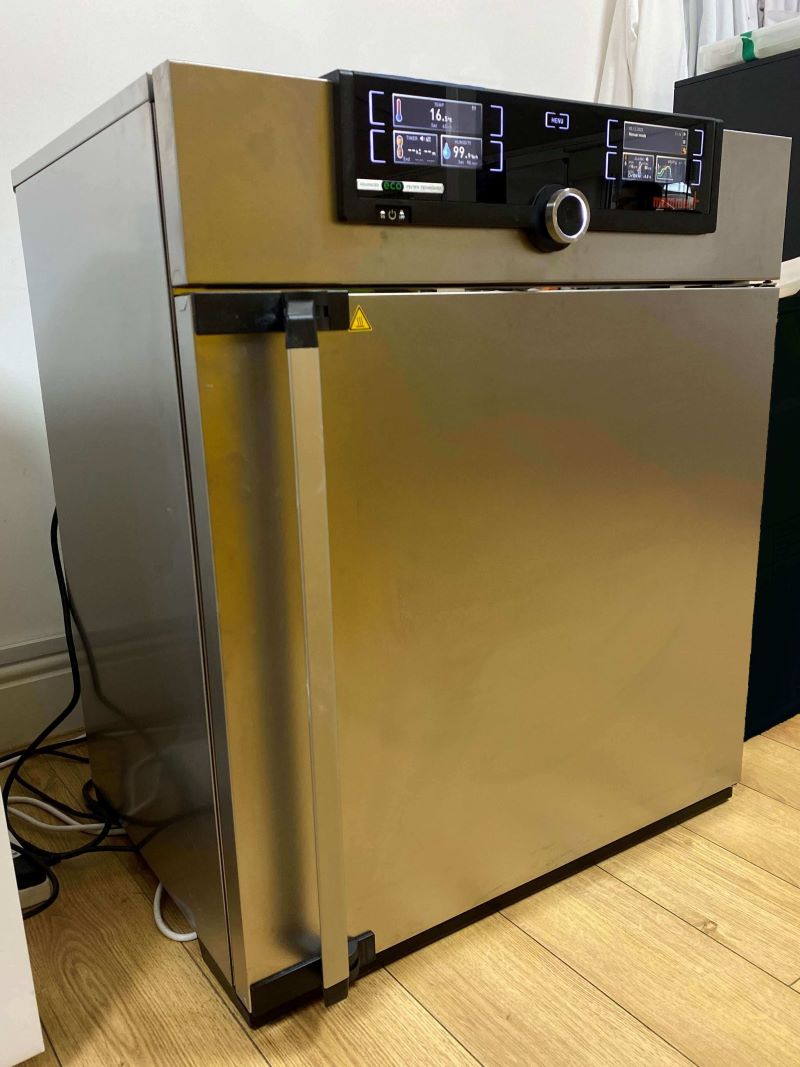
The Centre for Industrial Rheology’s combination of the climatic chamber and dynamic powder flowability instruments empower unparalleled insights in analysing powder behaviour across diverse temperature and humidity conditions, enabling tailored solutions with exceptional detail and reliability.
For the purpose of this study, we describe caking in terms of a reduction in flowability, in this specific instance due primarily to the addition of moisture via elevated humidity. There does exist the potential for moisture addition in this way to reduce the flowability of the powder without instigating the semi-permanent bridges we would associate with a defined caking behaviour. One example of this would be a moisture induced increase in cohesion between powder particles, essentially making each particle more “sticky” which would lead to a decrease in flowability. It is often possible to differentiate between caking and other flowability reducing behaviours, and this is discussed later in this case study.
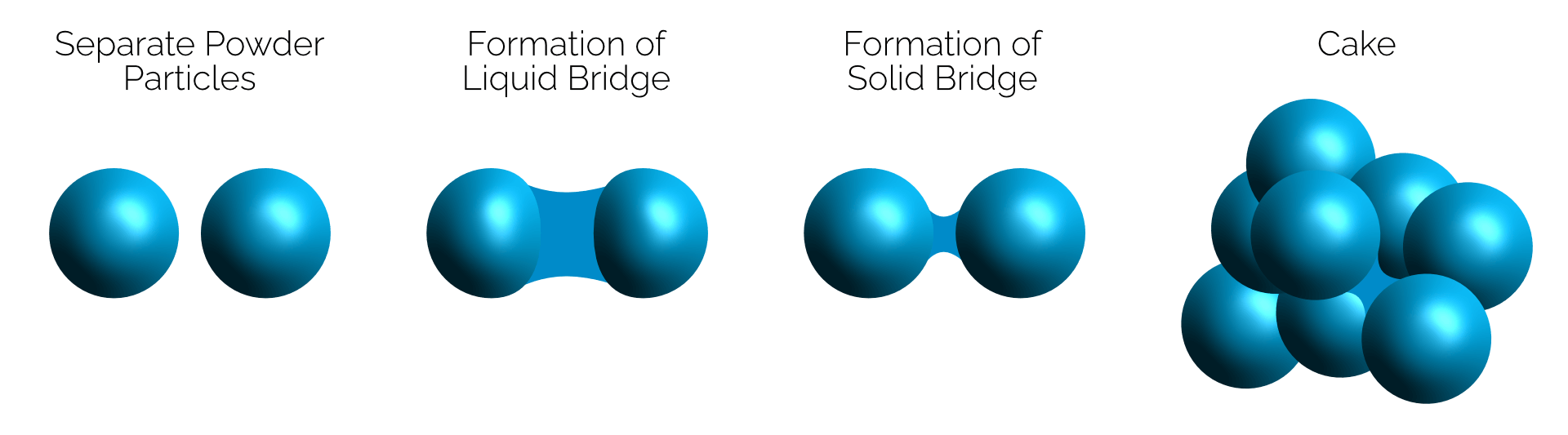
Initial Stability Test – Setting a Baseline Measurement
A baseline measurement is necessary to first ascertain the flowability of a powder prior to the induction of caking. To this end the stability measurement described earlier, incorporating the kinetic conditioning, is performed on the sample. The test was performed under appropriate conditions, traversal completed multiple times with kinetic conditioning performed prior to each traversal. This generates flowability snapshot as well as examining any non-humidity-based instability, which would need to be considered later on in the study.
In this case, we find the powder to be relatively flowable returning generally low Total Energy values, as well as displaying a small amount of instability from measurement 1 to measurement 2, over which the flow energy of the powder decreases, before reaching a stable plateau.
Stability measurement of a single paracetamol blend with no humidity conditioning.
Addition of a Drying Step in Resolving Problematic Caking
With an initial assessment of the flowability of the powders completed, testing was performed on aliquots of the powder which had been subjected to humidity conditioning. In these cases, the powder was first loaded into the test vessel and a kinetic conditioning step performed. The vessel was then removed from the instrument and inserted into a pre-humidified climate chamber set to hold 25°C, 90% RH. The sample was held at these conditions for a period of four hours. Following this, one vessel was removed from the climate chamber and immediately tested, whereas a second was allowed to equilibrate to ambient conditions (around 22°C, 40% RH) for a period of 90 minutes prior to testing.
The aim of this test was to ascertain the role of “drying” in the formation of the cake. Whilst we see an increase in flow energy for the humidity conditioned sample, the effect is much greater when the conditioning is followed by a drying step. It should be noted that for these observations we are particularly interested in the flow energy of step one, the first traversal of the vessel. This is the step where any significant cake, and the breakdown thereof, is most likely to be observed in the flow energy.
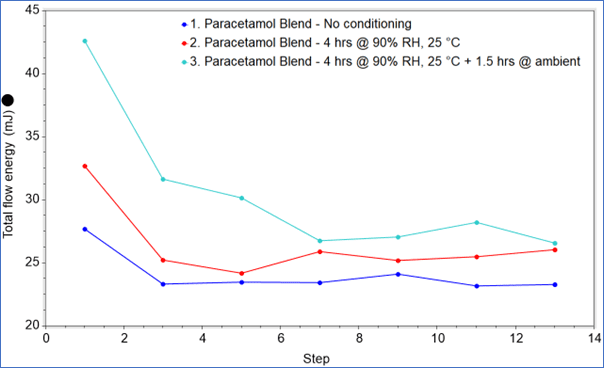
Increased Conditioning Time Leading to Lower Powder Flowability
Building upon the observed impact of the drying step in encouraging caking, the decision was made to maintain this step throughout the remainder of the testing. Further tests were performed incorporating gradually longer conditioning times. A large change in flow energy between an unconditioned and 4-hour conditioned sample is observed, as well as between a 16-hour conditioned sample and a 48-hour conditioned sample. Very little difference is found however between the 4- and 16-hour conditioned samples.
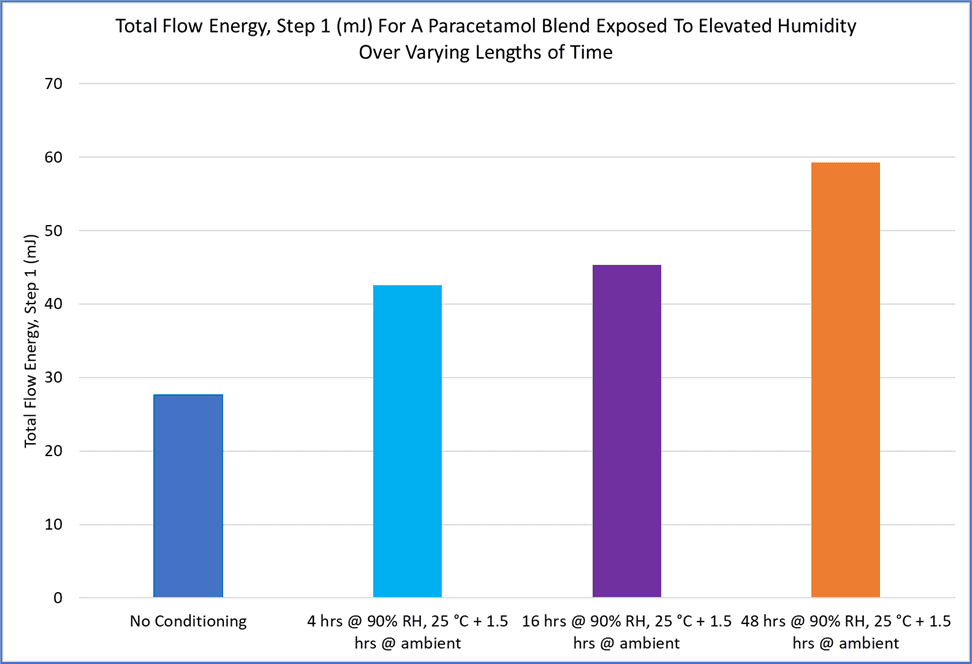
A Further Analysis into the Breakdown of Caked Powder
Examination of the total flow energy of the first run allows for a clear examination of the degree to which the powder has caked, as a function of decreasing flowability. Further analysis of the full stability curve allows for a more robust characterisation. By analysing the first few points, which equate to the first few traversals of the blade through the powder, we generate a picture of how the powder is changing, in terms of flowability, run-to-run. This provides an indication of the ease of which the cake is broken down. A powder which reaches an equilibrated flowability after a single traversal indicates a cake which was quickly broken down by a single traversal, versus multiple runs to equilibration indicating more time required to disrupt the semi-permanent bridges between particles. In this case, none of the samples display an exceedingly large number of steps required to reach equilibration, but there is a clear differentiation between the samples which were conditioned and dried, versus the remainder.
Secondly the equilibrated total flow energy, and specifically the difference between the conditioned and unconditioned samples, points to a permanent change in the flowability of the sample brought about by the conditioning steps. Once again, the drying step seems to be the largest contributor to this, although none of the samples subjected to conditioning are able to attain the flowability demonstrated by the initial, non-conditioned sample.
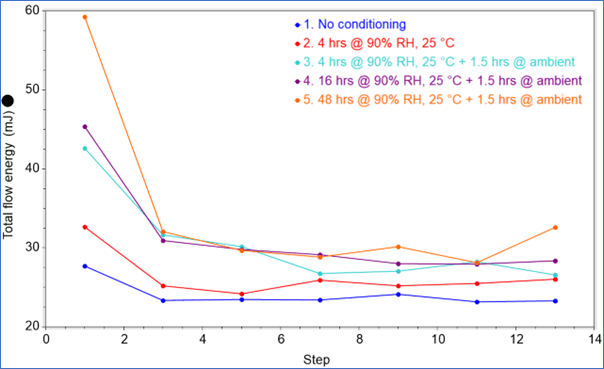
Analysis of Torque Versus Height in Identifying a Caked Powder
Total flow energy is calculated as a combination of the rotational torque and axial force encountered by the blade during its traversal through the powder column. Analysis of one or both of these individual contributors can often help to identify a truly “caked” powder from one that has undergone a general increase in cohesion throughout the powder mass. Further to this, often it is possible to identify a specific “type” of caking, for example a crust at the top of the vessel or multiple small pockets of agglomerates throughout the powder mass.
In this case, examination of the torque versus height data of the first downwards traversal for each of the tests reveals some interesting differences between the conditioning stages. The initial 4-hour conditioning with no drying time induces a higher torque throughout the majority of the measurement when compared with the unconditioned sample, with a slightly shallower gradient towards the end of the measurement. This likely indicates a general increase in cohesion throughout the powder bulk than a true “caking” behaviour.
For the samples with the drying step incorporated, a much steeper initial gradient is observed in all cases leading to an early torque peak at the top of the test vessel. This is a clear indicator of a crust of some kind having formed at the top of the vessel, which seems to be induced largely by the addition of a drying step. Once this initial crust has been cleared, the remaining torque data between the 4-hour and 16-hour conditioned samples remains fairly consistent.
For the 48-hour sample, we see both the strongest cake (evidenced by the height of the torque peak) and the deepest cake (evidenced by the depth to which the peak extends). Furthermore, the continued curve after the peak demonstrates a jagged or saw-toothed shape, often indicative of multiple small pockets of agglomerated throughout the powder mass.
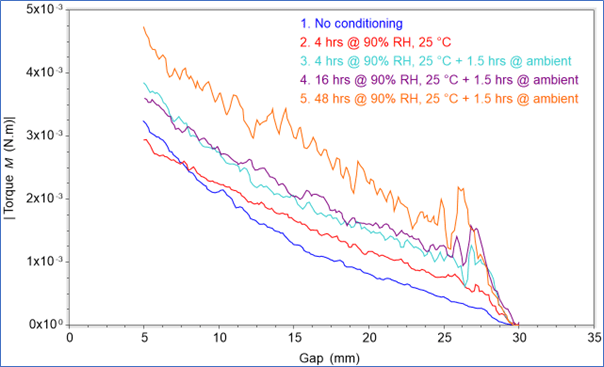
Conclusion
Dynamic flowability measurements provide a powerful tool for analysis of a range of powder caking behaviours. Whilst this study looks primarily at humidity induced caking, the method is easily adapted for looking into caking based on temperature, pressure, time consolidation or a number of these factors combined. The described methodology provides a quantifiable measurement of the degree to which a powder column has caked, measured as a reduction in flowability. Further to a quantification of the degree of caking, the method allows for exploration of the type of caking behaviour which has occurred and the breakdown profile of the cake.
These measurements will provide vital insights into process designers as well as powder formulators. This study examines the effect of a single condition on a single powder over a range of time points as an exploration of potential optimal or acceptable storage times for a powder. Once again, the method allows for a great degree of flexibility and a sample set or range of conditions could be selected so as to explore a range of other factors, such as the influence of a range of different humidities and temperatures over a set time period, or a single conditioning regime on a number of different powder formulations.
For further information about the testing services provided within this article, or if you have any questions, please feel free to get in touch.
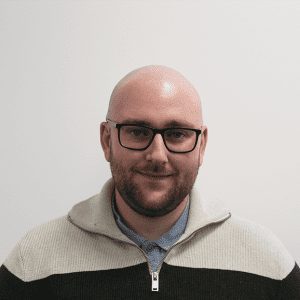